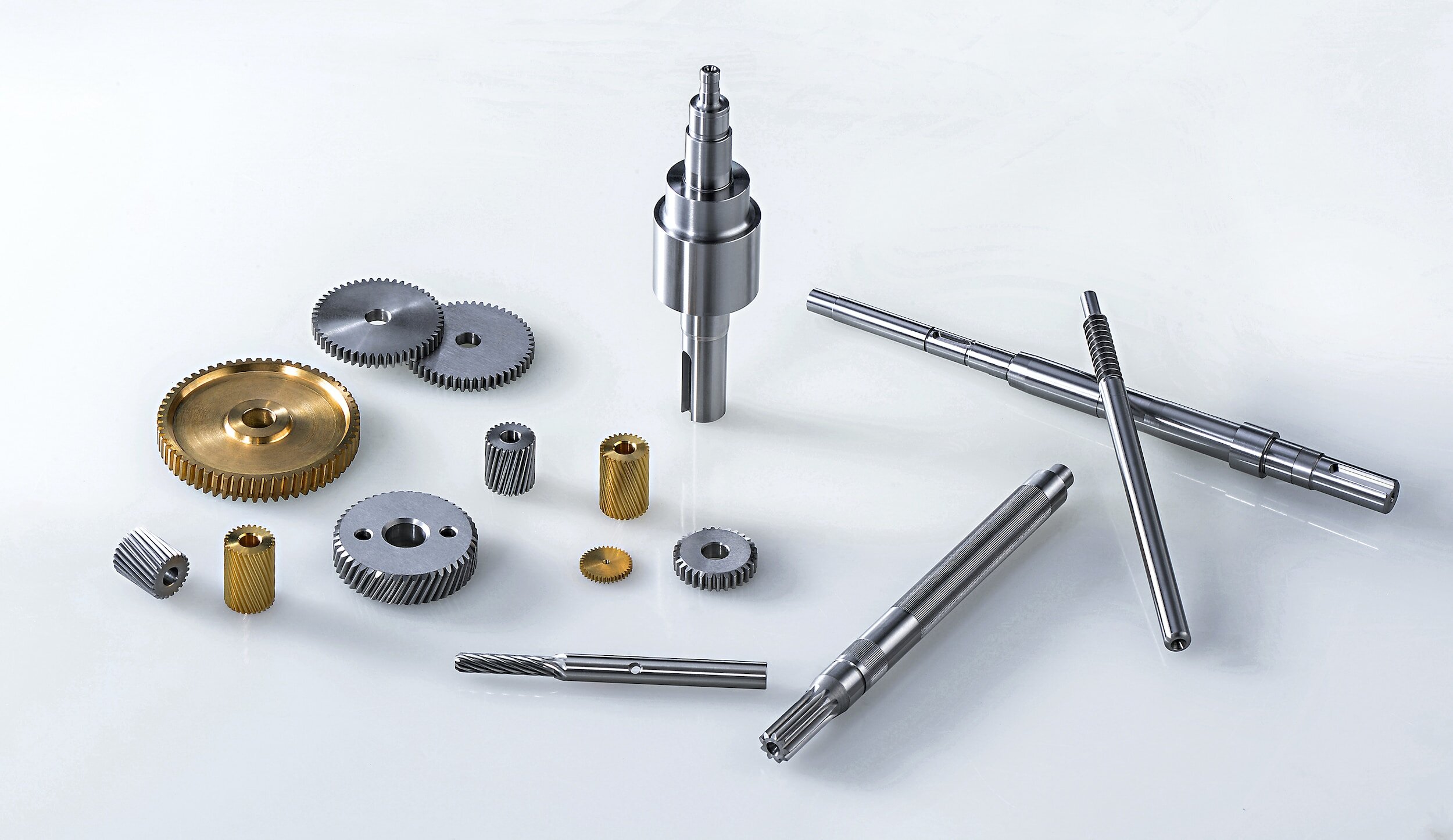
Innovative Solutions for
Rapid Prototypes.
Precision Routed Components
The advantages of CNC precision routing are plentiful and impactful. After the creation of a tool path and the programming of a machine, it has the capability to produce a part consistently and accurately, whether it's for a single piece or for a large-scale production run. The design and construction of CNC machines prioritize precision manufacturing and repeatability. This not only ensures cost-efficiency but also allows for seamless scalability for mass production. Moreover, CNC machines offer versatility, enabling them to handle an extensive array of materials, ranging from standard aluminum and plastic to more exotic ones like titanium. Consequently, they are the optimal choice for almost any manufacturing task. The adaptability and accuracy of CNC routing render it one of the most favored methods for crafting plastic and metal components, proficiently addressing a diverse set of product development requirements.
Available Materials:
High-Density Polyethylene
Type-I PVC
Copolymer Polypropylene
Polypropylene
Low-Density Polyethylene
Acrylic
Polycarbonate
Foam Filled PVC
ABS
Nylon
Carbon Steel
Aluminum
Stainless Steel
Titanium
CPVC
PVDF
Benefits of CNC Precision Routing
1. Precision and Accuracy: CNC routers are capable of cutting and shaping materials with incredibly high precision, ensuring consistent quality and accurate results.
2. Efficiency: By automating the cutting process, CNC routing significantly reduces production time, leading to increased efficiency and faster turnaround times.
3. Versatility: CNC routers can work with a wide variety of materials, including wood, plastics, foams, composites, and non-ferrous metals, making them versatile for various applications.
4. Complex Designs: With the ability to execute intricate and complex designs, CNC routing allows for the creation of detailed and ornate patterns that may be challenging to achieve using traditional methods.
5. Scalability: Whether producing a single prototype or mass-producing identical components, CNC routing provides scalability without compromising precision or consistency.
6. Cost-Effectiveness: While the initial investment in CNC equipment may be significant, the long-term cost savings from reduced material waste, labor costs, and enhanced productivity make it a cost-effective solution.
7. Reduced Errors: Automation reduces the likelihood of human error, minimizing material wastage and the need for rework, ultimately contributing to higher overall product quality.
8. Customization: CNC routing facilitates easy customization, allowing for personalized designs and tailored solutions to meet specific customer requirements.
9. Integration with CAD/CAM Software: Integration with computer-aided design (CAD) and computer-aided manufacturing (CAM) software enables seamless translation of digital designs into physical prototypes or products.
10. Prototyping and Rapid Iteration: CNC routing facilitates rapid prototyping and the ability to quickly iterate on designs, accelerating the product development process and reducing time to market.
11. Clean and Safe Operation: With proper safety measures in place, CNC routing offers a clean and safe manufacturing environment compared to traditional machining methods.
12. Environmental Considerations: CNC routing can minimize material waste through efficient nesting and cutting processes, aligning with sustainable and environmentally friendly manufacturing practices.
In conclusion, CNC routing offers a multitude of benefits, ranging from enhanced precision and efficiency to versatility and cost-effectiveness, making it a valuable manufacturing solution across various industries.